Rozwiązanie problemów jakościowych w procesach produkcyjnych jest niezwykle istotne dla osiągnięcia sukcesu przedsiębiorstwa.
Metoda QRQC, stanowi skuteczne narzędzie, które umożliwia szybką identyfikację, analizę i eliminację problemów jakościowych. W tym artykule przyjrzymy się bliżej tej metodzie i jak można ją wykorzystać w celu poprawy efektywności procesów produkcyjnych.
QRQC – wprowadzenie
QRQC jest strukturalną metodą rozwiązywania problemów, skoncentrowaną na szybkiej reakcji w przypadku wystąpienia problemów jakościowych. Jej założeniem jest skrócenie czasu reakcji i poprawa jakości w procesach produkcyjnych. Składa się z kilku kluczowych etapów, które są przedstawione poniżej.
Etap 1- Identyfikacja problemu
Pierwszym krokiem jest identyfikacja problemu. W tym etapie ważne jest dokładne zdefiniowanie problemu i określenie jego zakresu. Kluczowe jest również zrozumienie wpływu problemu na jakość i efektywność procesu produkcyjnego.
Najczęściej w tym celu wykorzystuje się metodę 5W2H. Więcej szczegółów na jej temat znajdziesz w osobnym artykule.
Etap 2 – Analiza problemu
Po zidentyfikowaniu problemu przeprowadzamy analizę przyczyn problemów i skutków. W tym etapie wykorzystuje się różne narzędzia i techniki, takie jak diagram Ishikawy, analiza 5xWhy czy diagram Pareto.
Etap 3 – Szybkie działanie
Ważnym aspektem QRQC jest szybkie działanie w celu naprawy problemu. W tym etapie podejmuje się konkretne działania mające na celu eliminację przyczyn problemu. Kluczowe jest skupienie się na szybkim, skutecznym działaniu, aby zminimalizować wpływ problemu na proces produkcyjny.
Etap 4 Zapobieganie ponownym wystąpieniom
W tym kroku zajmujemy się analizą przyczyny problemu i opracowujemy działania zapobiegawcze mające na celu eliminację tych przyczyn. Ważne jest także monitorowanie procesu w celu upewnienia się, że problem nie powróci. Właśnie takiego podejścia wymagają od nas Nasi klienci w branży motoryzacyjnej. To był też powód, aktualizacji dla wymagania IATF odnoszącego się do rozwiązywania problemów jaki znajdziecie w usankcjonowanych interpretacjach.
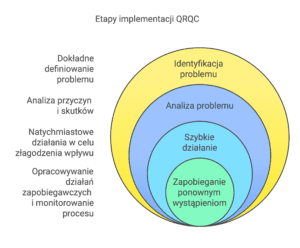
Jak QRQC jest powiązane z cyklem Deminga?
Pierwsze kroki rozwiązywania problemów w odniesieniu do QRQC są spójne do tych jakie znajdziesz w przypadku użycia Raportu 8D lub Raportu A3. Wynika to z faktu, że jest to jedna z trzech najbardziej popularnych metod rozwiązywania problemów stosowanych także poza branżą motoryzacyjną.
Dlatego nie ma żadnego zaskoczenia w tym, że podobnie jak dla tych dwóch technik, także metoda QRQC jest ściśle powiązana z cyklem Deminga. Znany jest on również jako cykl PDCA (Plan-Do-Check-Act) lub cykl ciągłego doskonalenia. Co ważne, stanowi on podstawę systemu zarządzania jakością i jest stosowany do ciągłego doskonalenia procesów i osiągania doskonałości organizacyjnej. Przy tej okazji polecam zapoznać się ze świetną książką „4 dni z doktorem Demingiem”, której recenzję znajdziesz tutaj.
Same powiązania QRQC z cyklem Deminga można przedstawić w kontekście poszczególnych etapów cyklu:
Planowanie (Plan)
Etap planowania odnosi się do identyfikacji problemu, zdefiniowania celów i określenia zakresu działań mających na celu rozwiązanie problemu. Określa się w nim również strategię i plan działania. Planowanie w QRQC jest zatem zgodne z pierwszym etapem cyklu Deminga, który zakłada ustalenie celów i planowanie działań.
Wykonanie (Do)
Etap wykonania odnosi się do realizacji zaplanowanych działań w celu eliminacji problemu jakościowego. Skupia się na skutecznym wdrożeniu działań zapobiegających powtórzeniu problemu. Jest to zgodne z drugim etapem cyklu Deminga, który zakłada wdrażanie działań zgodnie z ustalonym planem.
Sprawdzanie (Check)
Sprawdzanie odnosi się do monitorowania skuteczności działań i oceny, czy problem został rozwiązany w satysfakcjonujący sposób. Mamy tutaj do dyspozycji analizę wyników, porównanie ich z oczekiwaniami i ocenę, czy cele zostały osiągnięte.
Działanie (Act)
Odnosi się do wprowadzania działań zapobiegawczych. W tym etapie podejmuje się konkretne kroki mające na celu usunięcie przyczyn problemu. Działanie w QRQC jest zgodne z czwartym etapem cyklu Deminga, który zakłada wdrożenie zmian w celu ustanowienia nowych standardów i zapobieżenia powtórzeniu problemu.
Jak widać oba podejścia koncentrują się na ciągłym doskonaleniu i poprawie jakości. QRQC wykorzystuje cykl Deminga jako ramę odniesienia do identyfikacji problemu, planowania działań, realizacji, monitorowania wyników i wprowadzania działań zapobiegawczych w celu rozwiązania określonych problemów.
Jak QRQC wykorzystuje zasadę San Gen Shugi ?
San Gen Shugi jest jednym z narzędzi zarządzania jakością stosowanym w japońskiej kulturze organizacyjnej. QRQC wykorzystuje San Gen Shugi, obejmując następujące trzy zasady:
Genba
Oznacza „miejsce”. Z punktu widzenia QRQC, odnosi się do konieczności bezpośredniego przebywania na miejscu, gdzie występuje problem, oraz analizy rzeczywistych danych i informacji związanych z tym problemem. Wszystko ma na celu zrozumienie sytuacji.
Kiedy pracowałem w zakładzie tyskiego Fiata, ówczesny dyrektor zakładu zawsze pytał się pracownika odpowiedzialnego z rozwiązanie problemu czy udał się do Genby:)
Genbutsu
Oznacza „przedmiot”. Genbutsu podkreśla znaczenie koncentrowania się na konkretnej sytuacji i konkretnych miejscach, gdzie występuje problem. Skupia się też na badaniu bezpośrednio części, maszyn, procesów lub miejsc, w których problem się pojawił, aby zidentyfikować i zrozumieć przyczyny.
Genjitsu
Oznacza „rzeczywistość” i odnosi się do konieczności skoncentrowania się na rzeczywistości i faktach związanych z problemem. Dodatkowo opiera się na danych, dowodach i obserwacjach, aby podejmować decyzje i wprowadzać skuteczne działania naprawcze.
Korzyści zastosowania QRQC
Zastosowanie tej metody przynosi liczne korzyści i pozytywne rezultaty. Należą do nich przede wszystkim:
– Znaczące zmniejszenie występowania problemów jakościowych poprzez skoncentrowanie się na identyfikacji i eliminacji ich przyczyn. Tym samym mamy możliwość redukcji strat oraz kosztów.
– Ułatwienie szybkiego i skutecznego rozwiązywania problemów.
– Przyspieszenie i usprawnienie przekazywania informacji o problemach oraz skutecznych sposobach ich eliminacji. Pozwala nam to na zminimalizowanie strat czasu operacyjnego i zasobów.
– Eliminowanie ryzyka powtórnego wystąpienia raz rozwiązanych problemów poprzez wprowadzanie działań zapobiegawczych. Najczęściej przeprowadzane jest to przez zdefiniowanie nowych standardów. Odpowiednikiem tego działania w Raporcie 8D jest krok D7.
– Ulepszanie projektów opartych na danych dotyczących wcześniejszych błędów, co przyczynia się do ciągłego doskonalenia procesów i produktów.
– Podnoszenie umiejętności kadry w zakresie rozwiązywania problemów poprzez szkolenia i współpracę zespołową w ramach QRQC.
– Zwiększenie poczucia odpowiedzialności pracowników zespołów produkcyjnych poprzez zaangażowanie ich w procesy identyfikacji, analizy i rozwiązywania problemów jakościowych
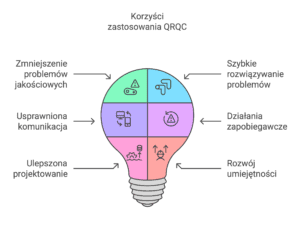
QRQC znalazło zastosowanie w wielu branżach i przyniosło pozytywne korzyści. W motoryzacji, implementacja tej metody doprowadziła do znaczącego zmniejszenia liczby reklamacji i poprawy jakości produktów. Podobnie w branży elektronicznej – szybka identyfikacja i eliminacja problemów produkcyjnych były jednym z argumentów do wdrożenia tej metody.
Wyzwania podczas wdrażania QRQC
Implementacja może napotkać pewne wyzwania. Najczęściej mowa będzie o braku pełnego zaangażowania zespołu lub trudności w identyfikacji głównych przyczyn problemów. Ważne jest jednak przestrzeganie najlepszych praktyk, takich jak skuteczna komunikacja w zespole, regularne przeglądy postępów (follow-up’y) i ciągłe doskonalenie tego procesu rozwiązywania problemów.
Niezaprzeczalnie strukturalne podejście stosowane w tej metodzie, skoncentrowane na szybkiej reakcji i eliminacji problemów, przyczynia się do poprawy jakości, efektywności i wyników przedsiębiorstwa.
Dariusz Kowalczyk