Każda organizacja rozpoczynająca współpracę z klientem z branży motoryzacyjnej musi być świadoma, że w trakcie fazy uruchomieniowej jego przedstawiciel zaplanuje w zakładzie produkcyjnym dedykowany audyt procesu.
Audyt klienta może zostać przeprowadzony, gdy bieżący dostawca dostarcza komponenty zawierające charakterystyki bezpieczeństwa przy nowych uruchomieniach. Może mieć również mieć miejsce, gdy klient, bazując na wcześniejszej ewaluacji scoringu, uznaje za konieczne przeprowadzenie weryfikacji bezpośrednio w jego zakładzie. Odbywa się to w trakcie fazy poprzedzającej produkcję seryjną.
Z tego powodu warto do takiej wizyty odpowiednio się przygotować. Należy także dodać, że gotowość do uruchomienia produkcji spoczywa na wielu obszarach, łącznie z tymi, które nie dotyczą bezpośrednio produkcji. Główne elementy, na których powinna się skupić firma są przedstawione poniżej.
Przegląd reklamacji 0-km wystawionych przez zakład produkcyjny oraz analiz zwrotów gwarancyjnych
Powyższe podejście ma zastosowanie w przypadku, gdy z danym klientem współpracujemy od wcześniejszych uruchomień. W organizacjach tym obszarem z reguły zajmuje się osoba odpowiadająca za jakość klienta. Niemniej jednak w przypadku kompleksowych wyrobów można się spotkać z rozdzieloną strukturą.
Każdy klient bezpośrednio przed wizytą u dostawcy ma możliwość zapoznać się ze statusem danych reklamacji, dlatego powinniśmy zadbać o to aby wszystkie akcje dotyczące działań tymczasowych (ICA – Interim Contaiment Actions) oraz działań definitywnych (PCA – Permament Corrective Actions) były w bazie klienta bezpośrednio zaktualizowane, np. w formie raportu 8D lub Kaizen.
Natomiast inaczej wygląda sytuacja w przypadku zarządzania zwrotami gwarancyjnymi. Oprócz dedykowanych wymagań specyficznych, każdy z klientów precyzuje odpowiednie wymagania jakie mają być spełnione w tym zakresie. Oczywiście w odpowiednich dokumentach audytowych.
Audyt klienta w odniesieniu do badań rekwalifikacyjnych
Powyższe zagadnienie jest obecnie stosowane bez wyjątku zarówno dla bieżących jak i nowych dostawców. Obszar ten wymaga dodatkowej uwagi nie tylko ze względu na wymagania poszczególnych klientów, ale też z powodu odpowiedniego wymagania IATF – 8.6.2. Kontrola wymiarowa i badanie funkcjonalności. Definiuje on, że wyspecyfikowane testy, które powinny obejmować dokumentację projektową, powinny się znaleźć w Planie Kontroli dostawcy.
W CSR’ach jest podana informacja odnośnie częstotliwości wynoszącej obecnie 1 rok. Oczywiście podczas spotkań jest możliwa odpowiednia ich negocjacja z klientem.
Warto przy tej okazji wspomnieć o innym kluczowym dokumencie, którym jest Supplier Product Validation. Dlaczego? Ponieważ to właśnie w nim określamy, jakie testy należy przeprowadzić w ramach rekwalifikacji.
W przypadku grupy VW standardowa częstotliwość wynosi 3 lata. Natomiast całkowicie odmienne podejście stosuje GM. Ten klient podaje, że w przypadku braku uzgodnień z danym działem odnośnie częstotliwości, nie ma w tym zakresie żadnych wytycznych.
W przypadku takiego scenariusza istotne jest, aby udokumentować i przedstawić odpowiedni dowód na uzgodnienie. Ten dokument będzie kluczowy w przypadku przeprowadzania audytu przez jednostkę certyfikującą, stanowiąc potwierdzenie zgodności z wcześniejszymi ustaleniami.
Audyt klienta vs. przegląd dokumentacji PFMEA/ Plan Kontroli / Flow Chart
Audyt klienta zwykle rozpoczyna się od zapoznania z dokumentacją dotyczącą danego projektu. Należy do niej sprawdzenie PFMEA, Planu Kontroli oraz Flow Chartu. Informacjami wejściowymi do zaprojektowania procesu produkcyjnego jest Flow Chart oraz FMEA projektu. Czasami nazywamy go również FMEA konstrukcji lub designu.
Natomiast danymi wejściowymi dla Planu Kontroli są informacje zawarte w PFMEA odnoszące się do czynności mających wpływ na zmniejszenie występowania problemu lub zwiększenia jego wykrywalności.
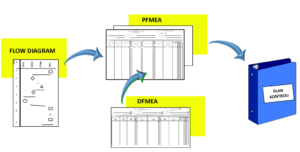
Biorąc pod uwagę połączenie tych dokumentów, musimy uwzględnić następujące wspólne elementy:
– numeracja poszczególnych operacji (we wszystkich trzech dokumentach)
– nazwa operacji produkcyjnych (we wszystkich trzech dokumentach)
– symbol charakterystyki specjalnej (obligatoryjnie w PFMEA oraz Planie Kontroli)
– przewidziana kontrola łącznie z częstotliwością oraz czasookresem, która musi być spójna w PFMEA oraz Planie Kontroli. W szczególności istnieje potrzeba, aby wprowadzić odpowiednie działania eliminujące możliwość wystąpienia problemu na linii produkcyjnej.
W kontekście metodologii 8D, należy uwzględnić aktualizację dokumentacji w kroku D7. Przeprowadzamy ją w ramach działań prewencyjnych po wystawionej reklamacji. Jest to kluczowy etap, który pozwala na skorygowanie i uniknięcie podobnych problemów w przyszłości poprzez dostosowanie dokumentacji do zebranych doświadczeń.
Dodatkowo każda osoba, która zajmuje się obsługą danego klienta powinna zapoznać się z dodatkowymi wymaganiami dla tych 3 dokumentów.
Na przykład GM w PCPA uwzględnia aktualizację PFMEA w oparciu o dane gwarancyjne. W praktyce wprowadzamy te działania po przeprowadzeniu analizy (wymaganie 56).
Na stronie „Bezpłatne narzędzia” można bezpłatnie pobrać automatyczny formularz Excel z możliwością edycji.
Nazwa dokumentu: Check Lista – 50 działań do weryfikacji przed wizytą klienta – formularz Excel