Error proofing (EP) i Mistake proofing (MP) to techniki stosowane w celu minimalizacji błędów w procesach produkcyjnych. Ich głównym celem jest wykrywanie i eliminacja błędów w początkowych etapach procesu, zanim wpłyną one na jakość końcowego wyrobu gotowego.
Mistake proofing – znaczenie i rola z punktu widzenia detekcji defektów
Do mistake proofing zalicza się wszystkie narzędzia pozwalające na wychwycenie problemu wygenerowanego we wcześniejszej fazie procesu produkcyjnego. Najczęściej są to End of Line testery (EoL) albo do Dock Audyty (DA). Służą one do weryfikacji funkcjonalności i poprawności działania danego wyrobu gotowego.
Właśnie takie oprzyrządowanie pozwala nam sprawdzić, czy nasz wyrób jest zgodny. Jeśli wynik takiej weryfikacji będzie negatywny, oznacza to, że mamy już wygenerowany brak. Wynika z tego, że jest to działanie odnoszące się do detekcji. Mistake proofing pozwala nam zapobiec przedostaniu się niezgodnego wyrobu gotowego do klienta.
Oczywiście pod jednym ważnym warunkiem – jeżeli mamy go odpowiednio skalibrowanego. Dlaczego? Ponieważ może się też okazać tak, że w przypadku przykładowego End of Line testera lub też Dock Audytu lub też innej stacji znajdującej się na końcu linii produkcyjnej przed pakowaniem nasza stacja uległa rozkalibrowaniu i nawet sztuki niezgodne były wysyłane do klienta jako sztuki NOK.
Przykłady Mistake Proofing
Przykłady zastosowania mistake proofing znajdują się poniżej:
- test szczelności dla zbiornika paliwa. Zbiornik zanurzany jest pod wodą i sprawdzana jest ilość pęcherzyków powietrza pojawiających się na powierzchni.
- test szczelności dla przewodów paliwowych. Wykonywany poprzez weryfikację spadku ciśnienia w funkcji czasu
- testy przesuwu do przodu i do tyłu dla prowadnic przednich foteli samochodowych
- siła wysuwania oraz wsuwania zagłówka
- dla kolumny kierowniczej jest to pomiar tarcia symulując skręcanie kierownicą w prawo i w lewo
- weryfikacja prawidłowego działania lamp samochodowych
- weryfikacja, jaką prędkością opuszczana i podnoszona jest szyba samochodowa
Error proofing, czyli lepiej zapobiegać niż leczyć
Natomiast to, co my chcemy wdrożyć, to są wszystkiego typu rozwiązania error proofing. W języku japońskim określane są one jako Poka-Yoke. Technika ta polega na wprowadzeniu takich zmian w procesie produkcji lub projektowaniu produktu, które uniemożliwią lub znacznie utrudnią popełnienie błędu.
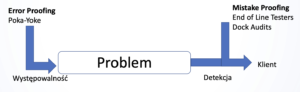
Dlaczego dla nas to jest tak istotne? Ponieważ w tym wypadku nie wyprodukujemy wadliwego wyrobu. Jak widać mamy więc dwie strategie dotyczące zarządzania kontrolą jakościową. Albo skupiamy się na detekcji albo na występowalności. Bardziej rekomendowana jest występowalność, także z punktu widzenia wymagań standardu IATF 16949.
Rodzaje Error Proofing
Jakie mamy rodzaje error proofingu? Jednym z częściej stosowanych rozwiązań w przemyśle motoryzacyjnym są poka-yoki mające kształt mechaniczny. Pozwalają nam one na jeden partykularny sposób ułożenia komponentu na stacji produkcyjnej.
Dzięki temu wymuszają odpowiednią pozycję danego wyrobu do wykonania na nim określonej sekwencji operacji (np. podczas przykręcania lub zgrzewania).
Inny często stosowany typ error proofing odnosi się do czujników zbliżeniowych. Ich celem jest weryfikacja obecności i sprawdzenie czy wszystkie komponenty, jakie są wymagane w danym cyklu produkcyjnym, znajdują się na danej stacji. Często ich zastosowanie jest powiązane z wizualizacją.
Na czym ona polega? Jeśli nie ma jakiegoś komponentu brakuje to:
- nie ma możliwości uruchomienia cyklu produkcyjnego
- świeci się czerwona lampka, informująca o braku obecności takiego podkomponentu i informacji o jego umieszczeniu na stanowisku. Dzięki temu dopiero wtedy będzie można uruchomić ten cykl.
Jako element wdrożenia strategii error proofing można też wdrożyć różnego rodzaju rozwiązania, które eliminują nam możliwość popełnienia pomyłki z punktu widzenia podobnych elementów. Najczęściej wytwarzanych obok siebie.
Tutaj wyróżnić możemy dwie kategorie:
- komponenty podobne z punktu widzenia zastosowanego koloru ( np. przewody elektryczne)
- komponenty posiadające podobną konstrukcję (np. na kolumnach kierowniczych, takimi bardzo podobnymi elementami są motory albo I-shafty)
Innym rodzajem error proofing jak i bardzo często jest wykorzystywany, w szczególności jeżeli chodzi o kwestie odnoszącą się do zgrzewania jest zliczenie elementów i informowanie o błędach. Jak to działa? W momencie kiedy pobiorę detal z lewej strony, umieszczam ją na zgrzewarce. Po procesie zgrzewania przykładam dłoń przez ramkę znajdującą się po prawej stronie i zgrzany komponent umieszczam w pojemniku.
Co nam to daje? Otrzymujemy informację, że ta dana część przeszła cały proces produkcyjny i nie została na przykład odłożona gdzieś przez operatora na stanowisku roboczym.
Wdrożenie Error Proofing
Jak widać, jeżeli chodzi o kwestię odnoszącą się do error proofing, istnieje dużo możliwości dla ich wdrożenia. Natomiast punktem wyjścia do ich implementacji jest to, co zawiera PFMEA czyli w projektowaniu procesu produkcyjnego. Jest to analiza ryzyka, wielokrotnie przywoływana przez wymagania IATF. Główne kryterium dotyczy tego jak duży wpływ dla klienta będzie miała wygenerowana wada w momencie, kiedy się ona do niego przedostanie. Na jakie pytania musimy odpowiedzieć?
- Jakim problemem będziemy się zajmować? Najczęściej skupiamy się na problemie związanym z bezpieczeństwem, homologacją, czy też z wymaganiami prawnymi
- Czy to będzie problem dotyczący braku lub też zmniejszenia funkcjonalności (no podnośnik szyby będzie działał wolniej i głośniej)
- Czy wada wiąże się z estetyką? Na przykład małe zarysowania, które są widoczne dopiero jak podejdę bliżej do zderzaka

O czym jeszcze warto pamiętać?
Samo wdrożenie Error Proofing lub Mistake Proofing oznacza, że jesteśmy w połowie drogi. Dlaczego? Ponieważ musimy pamiętać jeszcze o dwóch tematach.
- Każdorazowe wdrożenie ww. oprzyrządowania powinno skutkować stworzeniem odpowiednich przeglądów dla Utrzymania Ruchu. Przy jednej z reklamacji „pochwaliliśmy się” klientowi, że wdrożyliśmy EP, a po kilku miesiącach otrzymaliśmy reklamację na ten sam typ wady.
Okazało się, że nie uwzględniliśmy podczas wdrożenia odpowiedniej częstotliwości przeglądów prewencyjnych. Finalnie trzpień wchodzący w skład EP po kilku tygodniach zużył się na tyle, że pozwalał na zmianę orientacji bazowania podkomponentu podczas jego przykręcania.
- Kalibratory. Przed każdym uruchomieniem linii produkcyjnej, w celu sprawdzenia poprawnego działania EP i MP stosuje się odpowiednie części kalibracyjne. Tutaj musimy pamiętać, aby (podobnie jak samo error proofing) było weryfikowane z odpowiednią częstotliwością. Dodatkowo powinny one mieć odpowiedni kolor (jako element identyfikacji), który zapobiegałby jej wysłaniu do klienta wraz z wyrobami gotowymi.
Podsumowanie
Oczywiście wiadomo, że nie wszędzie jest to możliwe wdrożenie narzędzi error proofing, ponieważ czasem te End of Line testery, oprzyrządowanie, stacje robocze definiowane jako mistake proofing są wymagane w projekcie jako dodatkowa certyfikacja.
Dzięki temu wiemy, że nasz wyrób spełnia wszystkie wymagania z punktu widzenia założeń projektowych które stawia przed nami klient.
Dariusz Kowalczyk